CFD Simulation
CFD Simulation
Computational Fluid Dynamics
We use numerical solutions to analyze fluid flows and complex problems involving multiphase flows (such as liquid-liquid, liquid-gas, or gas-solid interactions), heat transfer or phase change
At TENSOR, we are experts in Computer-Aided Engineering (CAE) with a strong focus on Computational Fluid Dynamics (CFD). Our engineering approach allows us to solve a wide array of numerical simulation challenges, ensuring your projects achieve optimal performance and reliability.
Whether you’re dealing with complex fluid flows, thermal management, or multiphase interactions, our CFD simulation services are designed to provide precise and actionable insights. Trust us to enhance your design and engineering processes with state-of-the-art CFD solutions tailored to meet your specific needs.
servicesVersatile CFD simulation services for multiple industries, ranging from automotive and aerospace to energy and maritime, ensuring optimized designs and enhanced performance
Harness CFD simulations to enhance battery performance, ensuring optimal temperature regulation for prolonged lifespan and reliable energy output.
Navigate maritime challenges with precision, employing advanced fluid dynamics analysis to streamline vessel designs, minimize drag, and maximize fuel efficiency.
Employ CFD simulations to forecast aircraft systems’ behavior in terms of drag, lift, noise, thermal and structural stresses, and combustion.
servicesOur CFD simulation services effectively solve a range of critical challenges, including:
Fluid Dynamics Analysis
Streamlining designs to minimize drag and maximize fuel efficiency in maritime and other transportation sectors.
Thermal Management
Ensuring optimal temperature regulation for components, such as batteries, to prolong lifespan and improve reliability.
Performance Optimization
Enhancing the overall performance of products across various industries through precise simulations and analysis.
Design Verification
Ensuring that designs meet all necessary performance and safety requirements before physical production and testing.
servicesOur clients feel confident and assured, knowing their designs are optimized, compliant, and benefiting from:
Enhanced Efficiency
Streamlined designs lead to reduced drag and improved fuel efficiency, saving costs and boosting performance in transportation sectors.
Improved Reliability
Optimal temperature regulation extends the lifespan of components like batteries, ensuring reliable and long-lasting performance.
Superior Performance
Precise simulations and analyses enhance overall product performance across various industries, resulting in higher quality and customer satisfaction.
Regulatory Compliance
Thorough design verification ensures that all performance and safety requirements are met, reducing the risk of costly redesigns and compliance issues.
servicesKey Features of CFD Simulation Services
Turbulence Modeling
Accurately simulate the effects of turbulence in fluid flows, essential for predicting performance in various engineering applications
Multiphase Flow Analysis
Analyze the interaction between different fluid phases, such as liquid-liquid, gas-liquid, and solid-liquid flows, which is crucial for processes in chemical and petroleum industries
Thermal Management
Simulate heat transfer and thermal effects in fluid systems to optimize cooling and heating processes, ensuring component reliability and efficiency
Fluid-Structure Interaction (FSI)
Model the interaction between fluid flow and solid structures, helping predict and mitigate potential structural failures due to fluid forces
Acoustic Analysis
Evaluate noise and vibration characteristics in fluid systems, important for applications in automotive and aerospace industries to improve comfort and compliance with noise regulations
Combustion Simulation
Simulate chemical reactions and combustion processes to optimize performance and reduce emissions in engines and industrial burners
Shape Optimization
Optimize the geometry of components and systems to improve performance characteristics like drag, lift, and overall efficiency
HPC
Scalability
Utilize advanced HPC capabilities to run large-scale simulations efficiently, reducing computation time and enabling the analysis of complex models
servicesThe CFD Simulation Process
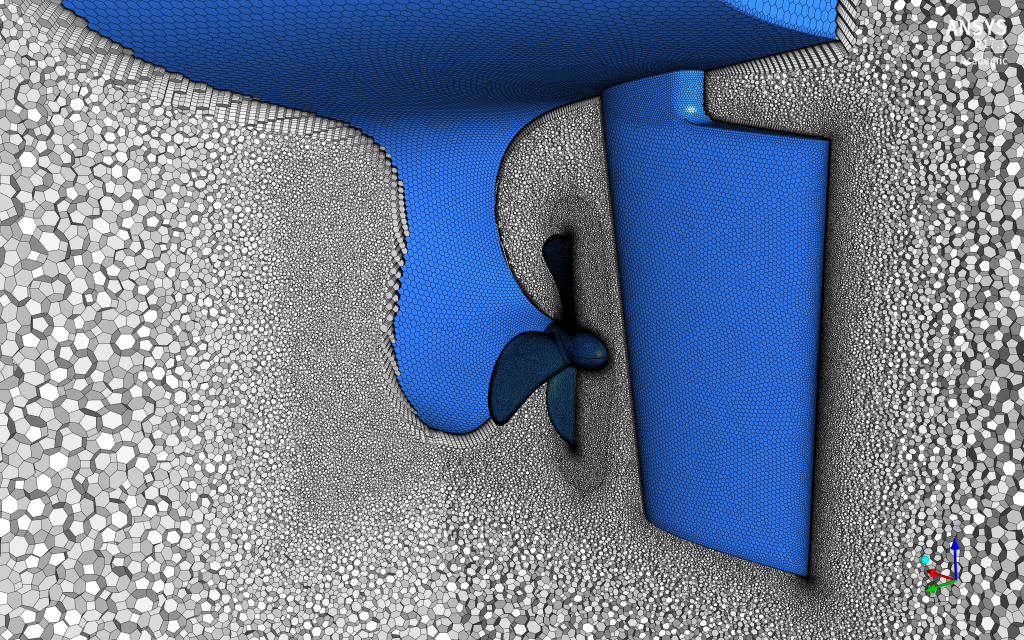
servicesStep 1 - Preprocessing
- Geometry Import: Importing the geometric model of the system or structure to be analyzed into the simulation software. This can involve CAD (Computer-Aided Design) models or other geometric representations.
- Model Simplification: Simplifying complex geometric models to improve computational efficiency without compromising accuracy. This may include removing unnecessary details or refining the mesh for better resolution in critical areas.
- Mesh Generation: Creating a mesh, or grid of discrete elements, over the geometric model to represent the physical domain. The quality and density of the mesh play a crucial role in the accuracy and efficiency of the simulation.
- Boundary Conditions: Specifying the boundary conditions that define how the system interacts with its environment. This includes constraints, loads, and other external influences that affect the behavior of the system.
- Material Properties: Assigning material properties to different parts of the model, such as stiffness, density, and thermal conductivity. These properties govern how the materials respond to applied loads and environmental conditions.
- Solver Setup: Configuring the simulation solver with appropriate settings and parameters to solve the mathematical equations governing the behavior of the system. This includes selecting the numerical methods, time steps, and convergence criteria.
servicesStep 2 - Numerical Simulation
Conducting the simulation based on predefined setups, closely supervising its progress to ensure it aligns with expectations, and adjusting parameters as necessary with minimal intervention.
In numerical simulations, the simulation process, also known as the analysis run, is the stage where the mathematical models representing the physical system are solved to obtain the desired results. This phase involves several key steps:
- Solver Execution: The solver, or simulation software, executes the numerical algorithms to solve the mathematical equations governing the behavior of the system. These equations may include differential equations representing physical laws such as conservation of mass, momentum, and energy.
- Iterative Solution: The solver iterates through the simulation time steps, updating the solution at each step based on the current state of the system and the applied boundary conditions. This process continues until the desired simulation time is reached or until convergence criteria are met.
- Time Stepping: For transient simulations, the solver advances the simulation in time, computing the system’s response at discrete time intervals. The size of these time steps may vary depending on the dynamics of the system and the desired level of accuracy.
- Numerical Methods: The solver employs numerical methods, such as finite difference, finite volume, or finite element methods, to discretize the continuous mathematical equations into a set of algebraic equations that can be solved computationally. These methods ensure accurate approximation of the system’s behavior.
- Boundary Conditions Enforcement: Throughout the simulation, the solver enforces the specified boundary conditions, ensuring that the system interacts with its environment as defined in the preprocessing phase. These boundary conditions may include applied loads, constraints, and external influences.
- Convergence Monitoring: The solver monitors the convergence of the solution throughout the simulation run, ensuring that the numerical solution stabilizes and achieves the desired accuracy.
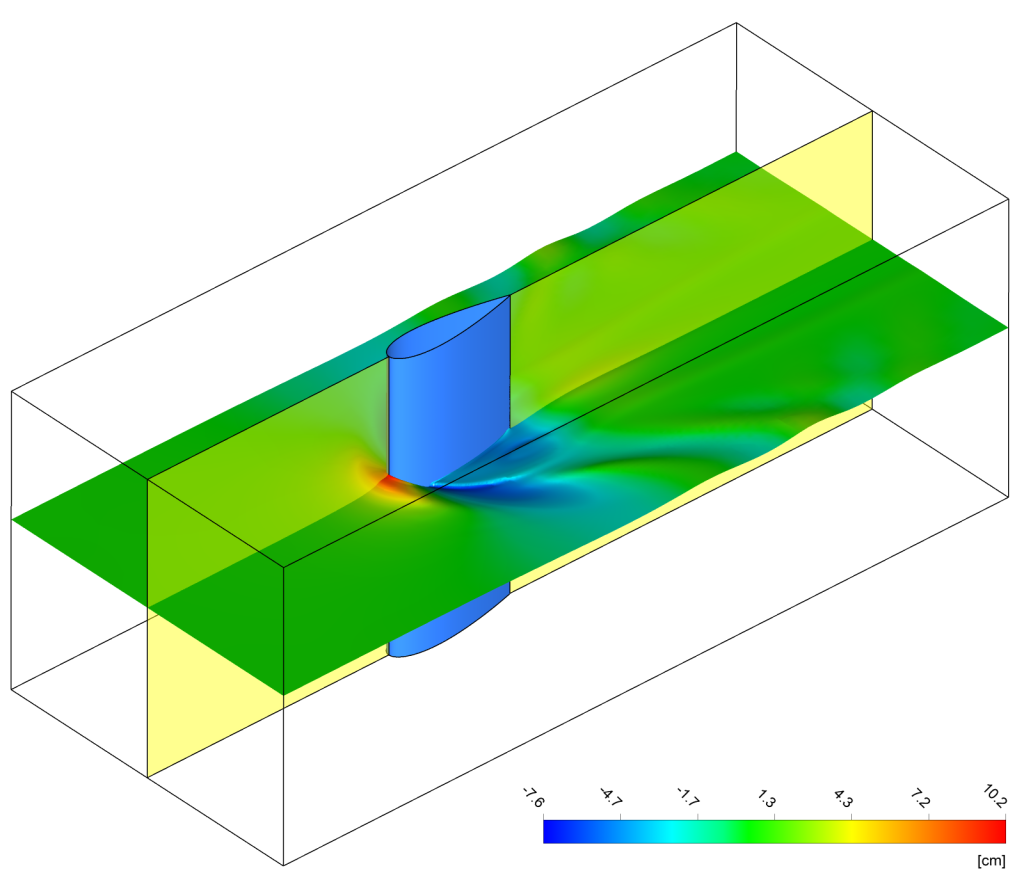
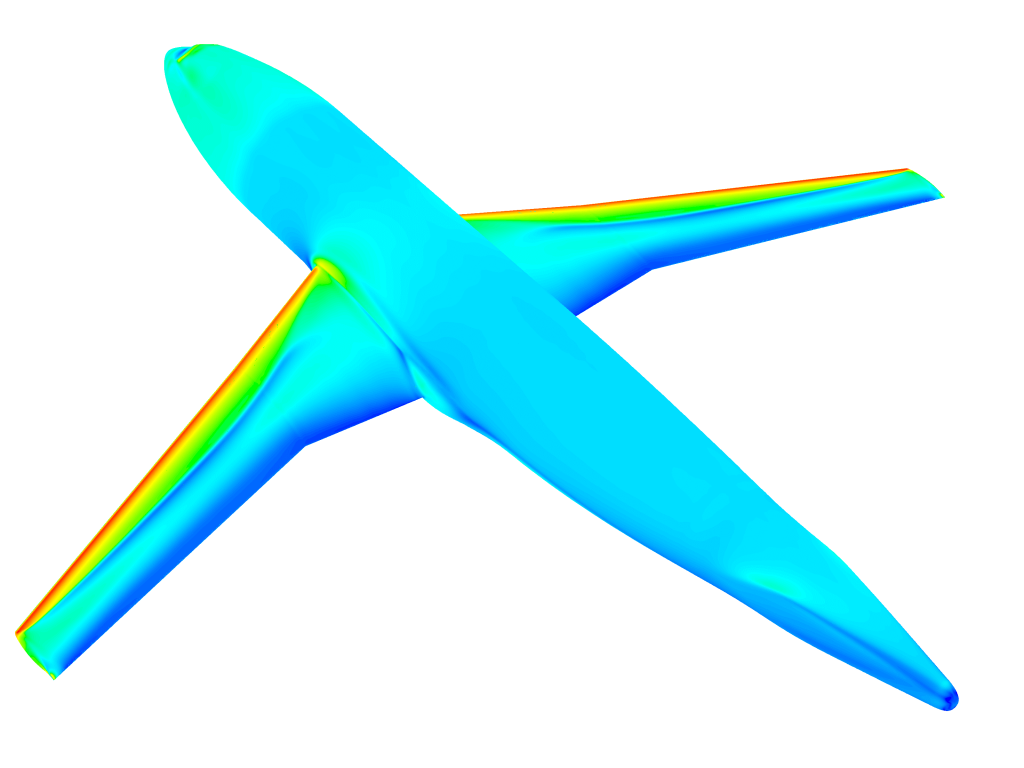
servicesStep 3 - Post-Processing
Extracting and analyzing the numerical results from the simulation, identifying and addressing discrepancies, and providing actionable recommendations for potential improvements or corrective actions.
In numerical simulations, the post-processing stage is a critical phase where the results obtained from the simulation process are analyzed, interpreted, and presented in a meaningful way. This phase involves several key activities:
- Result Visualization: The post-processing phase begins with the visualization of simulation results, which often include scalar fields (such as temperature, pressure, or velocity), vector fields (such as flow velocity), and other relevant quantities. Visualization techniques range from simple plots and graphs to more complex 2D and 3D renderings, contour plots, and animations.
- Data Analysis: Once the results are visualized, they are subjected to detailed data analysis to extract meaningful insights about the behavior of the simulated system. This analysis may involve computing statistical quantities, such as averages, maxima, and minima, identifying critical regions or features, and comparing results against design criteria or experimental data.
- Performance Evaluation: In many cases, numerical simulations are used to evaluate the performance of a system or design under specific operating conditions. The post-processing phase involves quantifying key performance metrics, such as efficiency, reliability, durability, or safety, based on the simulation results.
- Validation and Verification: It is essential to assess the accuracy and reliability of the simulation results through validation and verification exercises. Validation involves comparing simulation results against experimental data or analytical solutions to ensure that the numerical model accurately represents the real-world system. Verification, on the other hand, assesses the numerical accuracy of the simulation algorithms and discretization schemes.
- Decision Support: The post-processing phase provides valuable insights that can inform engineering decisions, such as design modifications, optimization strategies, or performance improvements. Engineers use the analyzed results to identify areas for improvement, validate design choices, and optimize system performance.
- Reporting and Documentation: Finally, the findings from the post-processing phase are typically documented in reports, presentations, or technical documents. Clear and concise reporting of simulation results, along with appropriate visualizations and analysis, helps stakeholders understand the implications of the findings and make informed decisions.
servicesStep 4 - Iterative Loop
Repeating the simulation process as needed to refine outcomes, address dysfunctions, or adjust to varying input data, ensuring continuous optimization and accuracy for meeting project requirements:
- Refinement: Continuously refining simulation results to improve accuracy and performance.
- Issue Resolution: Identifying and rectifying issues or dysfunctions through iterative adjustments.
- Adaptation: Adjusting for variations in input data to maintain relevance and accuracy.
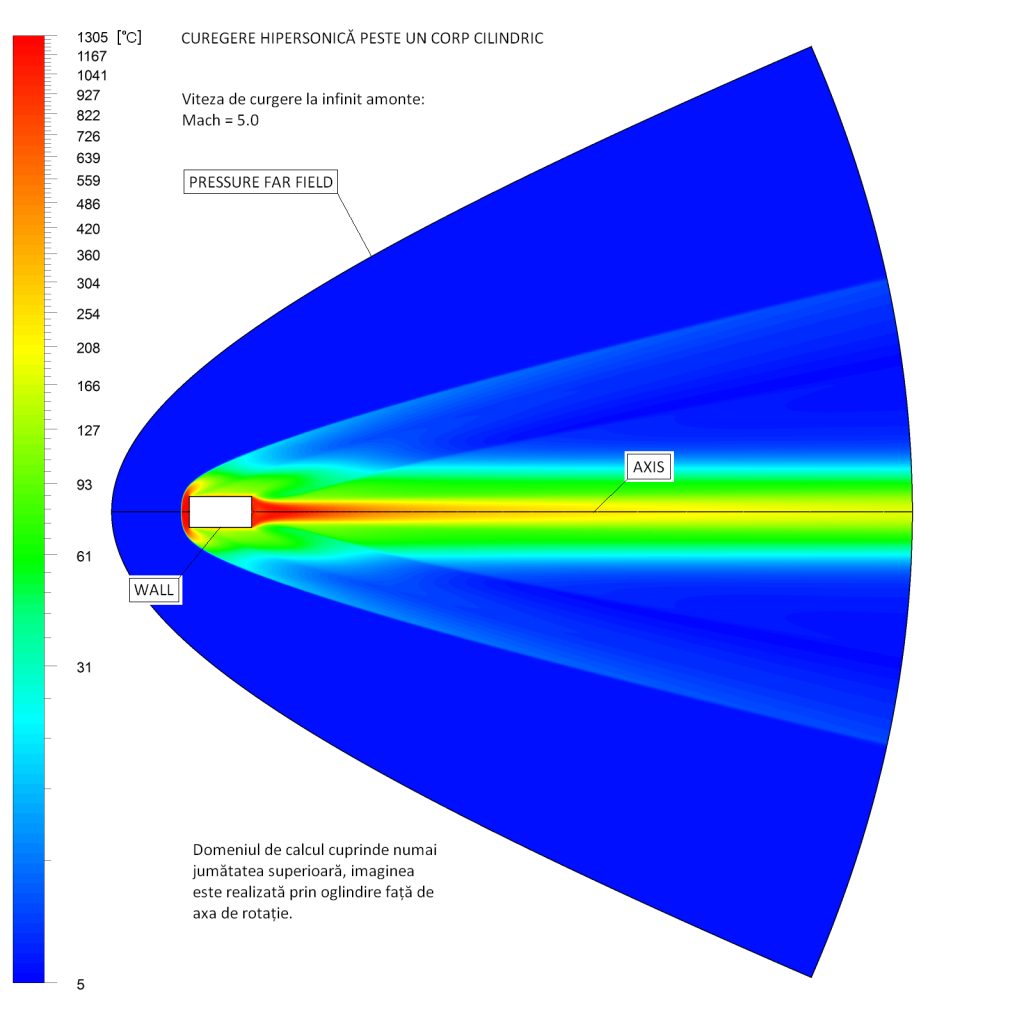