Introduction
In this article I direct my attention toward the study of inductance. The reason why this
measure is important to be studied is the same as previously mentioned with regard to capacitance,
which I have in depth investigated in a previous article: almost every interconnect
can be characterized up to a certain frequency as a lumped RLCG circuit. This is also the
case of parallel planes so ubiquitously spread in the power integrity field which can also
be characterized as a series (or parallel) LC circuit, where the C stands for parallel plate
capacitance and the L for inductance.
If capacitance is a simple and straightforward property which can easily be approximated
using the parallel plate formula as I have previously done in this article, inductance is the
rogue one from the LC pair. A simple approximation for inductance homologous to the
one for capacitance also exist but it assumes a uniform current distribution into the cavity.
Unfortunately, current density tends to be uniform only in narrow conductors while spreading
in different ways to follow the path of minimum impedance at high frequencies in wide
cavities.
In this article I investigate the inductance associated with wide cavities using ANSYS
HFSS 3D electromagnetic simulator and I also discuss how this property influences the
impedance profile of such a structure. The non uniform path that a current follows at high
frequencies can only be correctly investigated using a full-wave field solver. The existing
analytical approximations in the literature are also presented here along with their limitations.
Results from these formulas are also compared to the ones obtained from ANSYS HFSS.
Materials and Methods
In the case of a conductor modeled in the shape of a closed loop crossed by a current we
can extract the loop inductance with the equality from Equation 1 where Ψloop is the total
number of magnetic flux lines passing through the closed loop and I is the current crossing
the conductor. Subsequently, the total number of magnetic field lines can be obtained by
integrating over the whole surface B, the magnetic field density.

The formula from Equation 1 is often difficult to understand, almost never solved by
hand and only used in numerical algorithms. Eric Bogatin best describes inductance in [1] in
a much easier and understandable way: “Just as capacitance is a measure of the efficiency
of two conductors for storing charge at the price of voltage, inductance is a measure of the
efficiency of a conductor loop in storing magnetic field lines at the cost of current in the
loop”. Moreover, he also enumerates the complex mathematical principles that stand behind
the concept of inductance simplified in a few essential observations:
- magnetic field rings appear only as closed rings
- any current passing a conductor generates magnetic field rings closing around that conductor
- magnetic field lines do not interact with dielectric materials
- the number of magnetic field lines surrounding a conductor is proportional to the current through the conductor
- if the number of magnetic field lines around a conductor changes, a voltage will be generated across that conductor
- energy is stored in the magnetic field lines, the higher the number of field lines, the more energy being stored
In the incipient part of a design, simple analytical approximations are needed to estimate
properties such as inductance. The kind of approximations such as the parallel plate
capacitance should not be used for signing off a design. Exact expression that can accurately
calculate a figure of interest are preferred if possible. Unfortunately, in the case of loop
inductance we can only develop this kind of expression for three specific geometries: coaxial
cable, two round rods and a rod over a plane, none of which is close to parallel planes. For
any other structure the loop inductance can only be exactly calculated if the fundamental
definition is used.
Homologous to the parallel plate capacitance, an analytical approximation also exist for
the loop inductance of two parallel conductors separated by a dielectric. This is the expression
from Equation 2, where μ0 is the permeability of free space equal with 4 · π · 10 -7 H/m and
Len, w, h are the length, width and height of the structure. The product μ0 · h is named Lsquare and is the sheet inductance, how much inductance resides in a square from a specified
geometry.
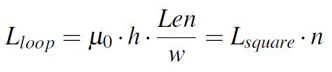
As the parallel plate capacitance formula has its limitations due to fringing effect investigated
in this previous article, so does the expression from Equation 2. This one is only
accurate for narrow and long conductors, where the current distribution is constant in the
whole surface. With other words, only geometries with aspect ratios w/h higher than 10
will lead to accurate results. For lower aspect ratios, transmission line approximations for
inductance should be used [2].
Equation 2 also gives us the three general design principles to reduce loop inductance:
lowering the length of the parallel conductors, making the conductors wider and bringing
them closer together. This is the reason why wide, closely spaced parallel planes are used in
power distribution networks in high speed circuit boards. Even if large power planes also
bring a higher parallel plate capacity, the low loop inductance that these large power plane
bring is by far a higher contribution than their capacitance in the design of a PDN.
Using Equation 2 to quickly investigate a simple narrow cavity of 80 MILs width, height
of 7.87 MILs and a length of 80 mm provided a result of 9.88 nH for the loop inductance.
Using also ANSYS HFSS to extract this inductance I obtain a value of 8.34 nH, close to
the initial estimate. Differences between analytical and simulation values were caused by
using Equation 2 at the margin of its applicability domain, for a structure with w/h 10.
For the same geometry I also performed a transient simulation by launching a 35 ns rise
time signal from a 5 MILs contact point situated at one end and saving the current density in
the upper plane. Observe in Figure 1 how the current spreads almost immediately into the
narrow plane. However, the few ps it takes the current to spread into the full width of the
structure contribute to a small non uniform density.
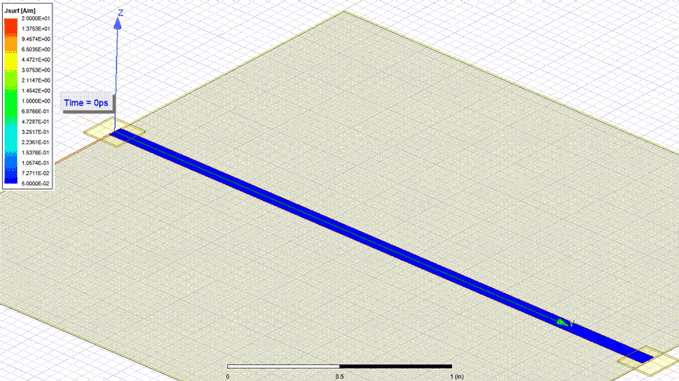
separation between planes (w/h ≈ 10) when a 35ns rise time wave is launched from one end
from a 5 MILs width contact point. Observe how the current almost immediately spreads
into the whole width of the narrow plane.
When the cavity is not long and narrow but wide, the current density in the copper planes
is by far uniform. When a signal in launched from the contact point into a cavity it spreads
radially until it hits the walls of that cavity, gets reflected and fades out in the end. At different
points into the cavity the current density differs, being higher near the contact point and
lower towards the margin of the cavity, leading to an inductance highly dependent of port
location. The loop inductance when the current spreads outward from a small contact region
is therefore refereed as the spreading inductance. Equation 3 is an analytical expression for
the spreading inductance of a cavity provided in [1] by solving the definition from Equation 1.

Equation 3 is only accurate for a circular cavity with the diameter Dcavity probed from
a central contact point with a diameter DVIA. The cavity is formed by two parallel planes
separated by a dielectric of height h. This geometrical limitation of a circular shape is a result
of integrating the original definition of inductance over a circular area [1]. However, it gives
an insight into the control knobs we have for lowering the spreading inductance: shorter
cavities and as closed as possible planes. Once again, notice how important is to have the
planes spaced as close as possible in power distribution networks.
As previously mentioned, spreading inductance is all about the the current distribution in
the planes when wide cavities are subjected to analysis. In order to better present the concept
of current density in wide planes I performed three transient simulations for a 80 mm square
structure with the planes separated by 7.87 MILs of dielectric material. I launched a 35 ns rise
time signal from the center, edge and corner of this structure through a 20 MILs contact point
and investigated the first 200 ps of current propagation through the structure. The results
are displayed in Figures 2, 3 and 4. Observe in these three cases how the current spreads
from the source as the ripples of water in a pond in four quadrants. When we restrict the
area at only two quadrants as is the case of the margin contact point from Figure 3, a higher
current density will appear leading to roughly twice as much spreading inductance (the exact
numbers are presented in the Dissemination and Results section). The same premises applies
when the contact point is situated in the corner, leading a four times higher inductance due to
the current spreading in only one quadrant.
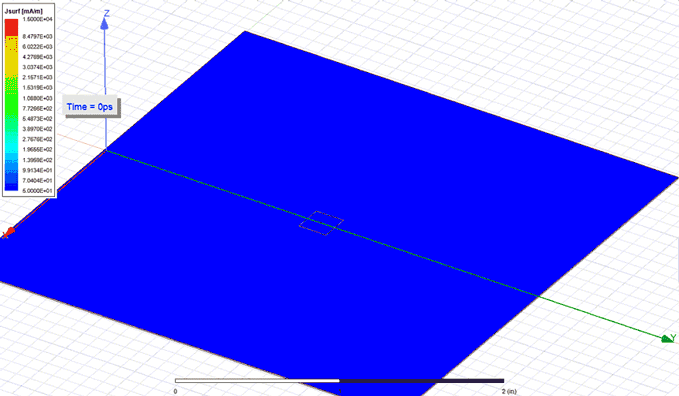
separation between planes when a 35ns rise time wave is launched from a 20 MILs width
contact point situated in the center. Observe how the current spreads 360° around the source
point.
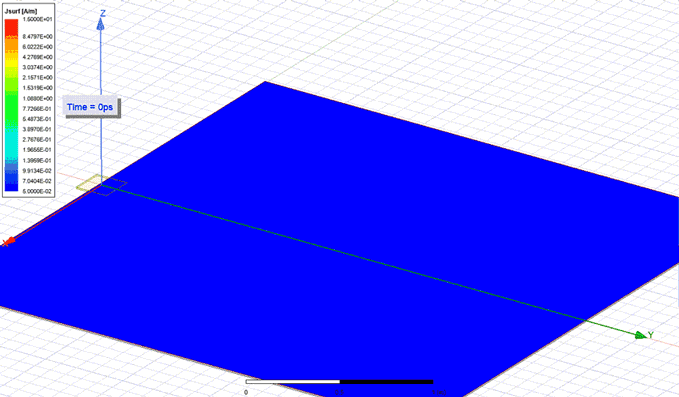
separation between planes when a 35ns rise time wave is launched from a 20 MILs width
contact point situated on one edge. Observe how the current can only spread 180° around the
source point.
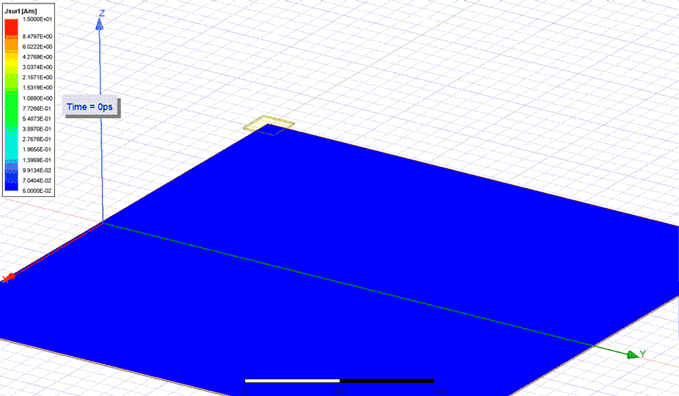
separation between planes when a 35ns rise time wave is launched from a 20 MILs width
contact point situated on a corner. Observe how the current can only spread 90° around the
source point.
The impedance profile of a cavity reveals tons of information regarding geometric
aspects and not only. Suppose we probe the same 80 mm square cavity from a contact point
located in its center, with no other shorting wall applied to its margins, what would be the
expected result? The impedance profile of the cavity will have three intervals, the first starting
at low frequencies dominated by the capacitance of the planes, Ccavity, the second dominated
by the spreading inductance, Lspread and the third where modal resonances take place in the
high frequency domain.
Focusing for now on the first two interval, we can easily approximate the cavity as a
lumped series LC circuit (or parallel if we were to short its edges with an perfect conductor
wall). The point separating the capacitive from the inductive behavior is nothing more than
the self-resonant frequency (abbreviated SRF) of a series LC circuit which can be calculated
using Equation 4.
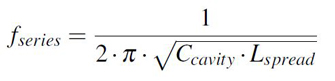
The capacitance of the cavity is independent of the probing location and can be accurately
calculated if the fringing effect is taken into account as discussed in this previews article.
However, the spreading inductance that in some cases can be calculated using Equation 3 is
highly influenced by the probing location. Subsequently, the SRF point will have different
values for different probing locations.
So far I have only discussed about the spreading inductance as seen from a contact point
placed in different locations of a structure looking into the cavity with the current traveling
radially outwards from that contact point. This is roughly the minimum series inductance the
current sees as it travels the cavity. Any other configuration will only increase its inductance.
Take for example a more practical case, the spreading inductance between two contact points
from the terminal of a SMD capacitor to the pad of a BGA. There are now two contact points
involved, the VIA below the BGA pin and the one next to or in the pad of the capacitor.
These two contact points lead to a higher density current which subsequently leads to an
increased spreading inductance.
A simple approximation for the spreading inductance from one point to another is
provided by Equation 5 [1]. This formula was developed based on the following premises:
the first contact point with a diameter d known is considered to be in the center of a circle
and the second one is placed on the margin of that imaginary circle. If the spacing of the two
points named s here is known, the diameter of the circle is also known as 2·s. The spreading
inductance from the center of this imaginary cavity would have the expression previously
presented in Equation 3 if only one point was involved but due to the current concentration
towards the second contact point, the result must be scaled with a certain scaling factor,
found in this analysis to be equal with 2.5. The final formula is provided in Equation 5.

Considering the premises that led to Equation 5, its limitations are quite clear: when the
spacing between the points becomes comparable to one length of the cavity, the spreading
inductance will in reality be larger than the one predicted by the analytical formula. This is
easily explained in this case since when one contact point of both are close to the margins of
the cavity, current crowding is no longer only caused by the two contact points but also by
the margin of the planes.
Equation 5 also gives insight about how the spreading inductance can be reduced with by
far the highest positive impact coming from lowering the spacing between planes. Bringing
the two contact points closer also has an impact but not as much as lowering the spacing
between planes. The interesting observation is that the contact point diameter has the same
influence as the distance between the two points: they both slowly influence the spreading
inductance with a small logarithmic dependency. This is also the main reason why multiple
VIA whole when connecting a capacitor to the power planes significantly reduce inductance.
Simulation setup
In this article I was interested to investigate spreading inductance and what limitations
do the analytical formulas presented in the previous section have. Using a spreadsheet I
implemented these formulas for different structures and compared analytical results with
the ones simulated in ANSYS HFSS. I created three parallel plane structures for this study,
two squares with the length of 80 mm and a circle with the diameter of also 80 mm. The
dielectric between copper planes was a classic FR4 with height of 0.1, 0.2 and 0.565 mm
depending of the study performed. Port size also has an important influence as previously
mentioned and since I also wanted to investigate this variation I used different port sizes of 5,
10 and 20 MILs.
Displayed in Figure 5 is the round structure I used to investigate the spreading inductance
when the cavity is probed from center. Only one lumped port was added in the middle of this
cavity and the impedance profile from 10 MHz to 1 GHz was simulated. Variations of 0.1,
0.2 and 0.565mm for height and of 5, 10 and 20 MILs for port width (what would be taken as
DVIA in Equation 3) were investigated. The impedance profile was expected to look like the
one of a series LC circuit, capacitive at low frequencies and inductive above the SRF point.
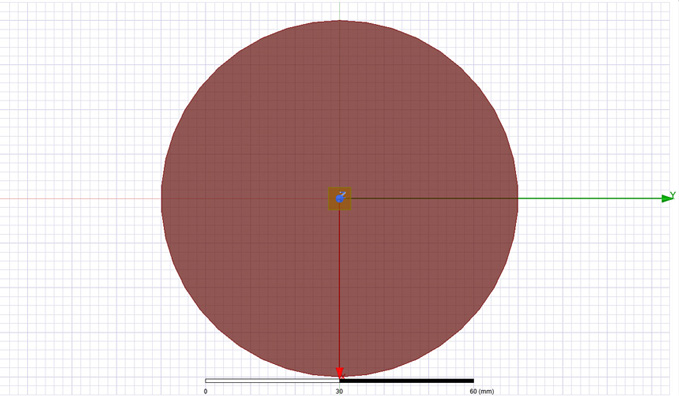
from the center and variations of height and contact point width are performed. D = 80 mm,
h = 0.1, 0.2 and 0.565 mm, PORT WIDTH = 5, 10 and 20 MILs.
Another geometry used in this investigation is the square one from Figure 6 with a length
of 80 mm, a fixed plane separation of 0.2 mm (also referred as height or dielectric height)
and a port width of 20 MILs. Using this structure I investigated what is the impact of port
location to spreading inductance. As mentioned in the previous section, this measure is
highly influenced by the current density with a higher spreading inductance expected in the
case of a port placed in the corner of the structure rather than when it is placed in the center.
The impedance profile was expected once again to look like the one of a series LC circuit, a
capacitive interval followed by an inductive one separated by a SRF point.
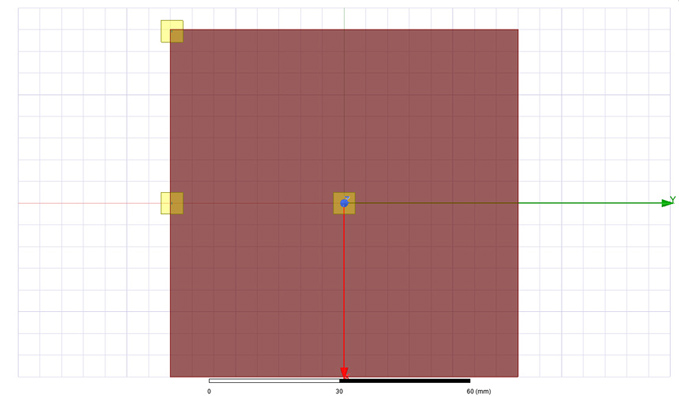
from different locations: center, margin and corner. L = 80 mm, h = 0.2 mm, PORT WIDTH
= 20 MILs.
The last structure investigated in this article is also a square one with the same parameters
(length = 80 mm, height = 0.2 mm). However, the setup was slightly different here. On the
median line of the cavity I created one fixed 0Ω short termination and one moving lumped
port as you can observe in Figure 7. Placing the port at different distances from the short
ranging from 50 MILs to 1000 MILs, I obtained multiple results used to evaluate the point to
point inductance. Moreover, I ran for every distance three simulations for port widths of 5,
10 and 20 MILs. The expected impedance profile is one of a parallel LC circuit this time,
due to the 0Ω short placed between the two copper planes, with the spreading inductance
being dominant in the low frequency interval.
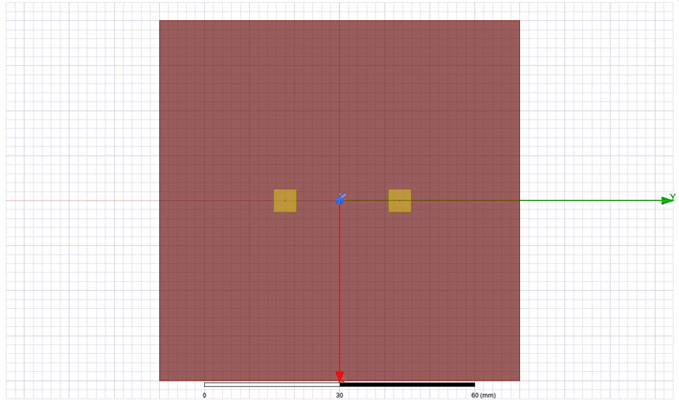
a square cavity when the points are far away from margins. Spacing between the two contact
point is varied from 50 MILs to 1000 MILs for three different contact point widths: 5, 10
and 20 MILs. L = 80 mm, h = 0.2 mm.
One last remark that I should make in this section is related to the meshing process.
Since the structures of interest were quite large, the adaptive meshing process that ANSYS
HFSS performs would have taken a serious amount of time until the point of convergence. In
order to speed up this process, I constrained the meshing algorithm to generate on a specific
area around the ports mesh elements with a maximum length of 3 MILs but without passing
the limit of 5000 elements on that specific area. This process named mesh seeding is used
to improve the mesh quality and speed up simulation time. Without the mesh seeding the
adaptive algorithm converged in 6 iteration in contrast with only 4 when seeding was applied.
You can observe in all the geometries presented in Figures 5, 6 and 7 a couple of small 5 by
5 mm yellow sheets representing the seeding areas. These squares are strategically placed
above ports based on the fact that in this specific location where energy enters and exits the
structure a denser mesh dramatically reduces iterations number [2]. Notice in Figure 8 how
the meshing algorithm was constrained to concentrate multiple mesh elements around the
ports.
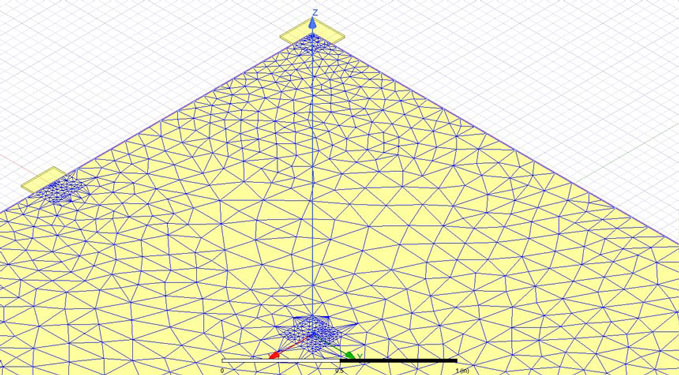
by ANSYS HFSS. Mesh seeding an area of 5 by 5 mm around ports reduced the iteration
number from 6 to only 4.
Dissemination and results
Using the geometry from Figure 5, the impedance profile was extracted for the specified
parameter variations and is presented in Figure 9. Notice how in the capacitive interval of this
profile we can distinct only three lines corresponding to three different capacitance values,
one for each height of 0.1, 0.2 and 0.565 mm. Needless to say the the highest impedance
value (lowest capacitance) corresponds to the highest plane to plane distance. The interesting
part of this profile stands in the second interval, where 9 different inductive lines are visible,
each corresponding to a combination of height and port size. By approximating the imaginary
part of this impedance with the one of a lumped inductor (L = Im{Z}/(2·π·f)) I extracted
the spreading inductance on a restricted interval between 0.70 and 1 GHz, these values
being visible in Figure 10. These inductance values are also listed in Table 1 along with the
numerical results give by Equation 3. The simulation and analytical data are well correlated
with small errors occurring for high plane to plane spacing.
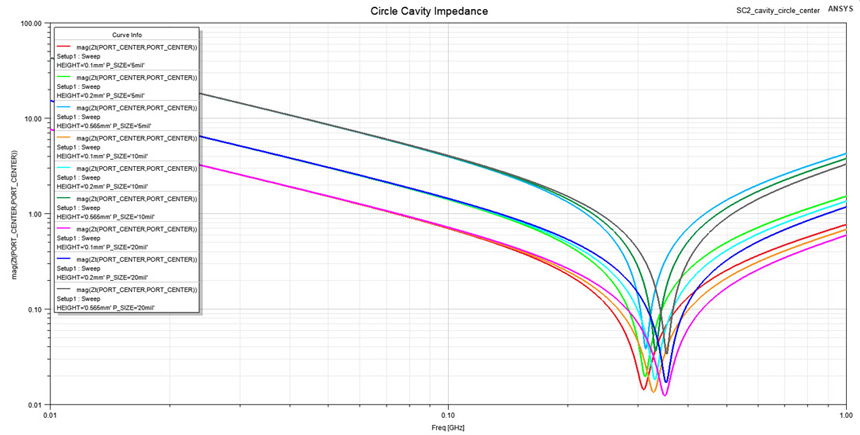
Observe how capacitance is only sensitive to dielectric height but spreading inductance is
sensitive to both plane separation and port width.
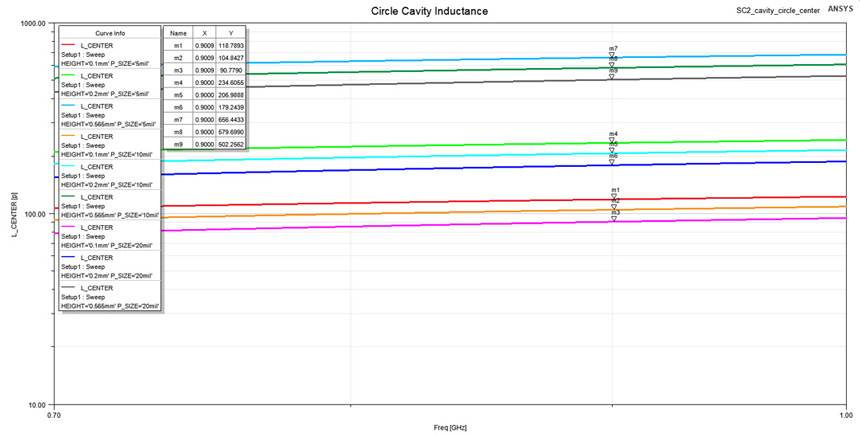
Figure 9. Notice how inductance is influenced by plane separation and and also port width.
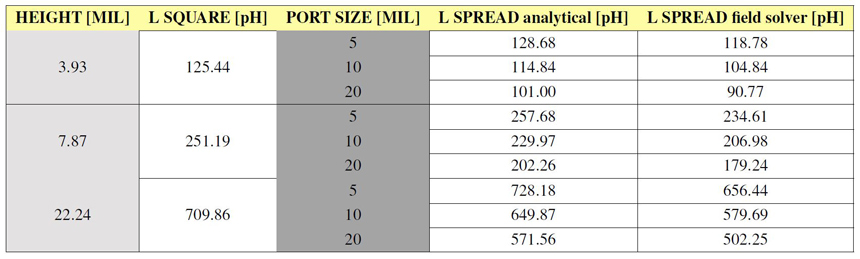
3D field solver results are obtained from ANSYS HFSS and analytical ones from Equation 3.
Moving to the second geometry studied in this investigation, its extracted impedance
profile is displayed in Figure 11. This plot reveals how contact point location alters spreading
inductance. Three locations were investigated: center, margin and corner of the square cavity.
Observe how in the capacitive interval there is no distinction between these three cases
since capacitance is independent of probing location. However, in the inductive interval
three different values stand up, one for each contact point. Subsequent, the SRF point of
each profile is different for each probing location in part. The third interval of an impedance
profile is also visible here, with resonances in planes starting at 0.81 GHz. The source of
these resonances are waves reflecting from the open edges of the cavity and occur at specific
frequencies where the length of the structure equals half of the wavelength of the radiation.
Resonances in the planes are not of interest in this article, but will however constitute the
subject of another future blog post.
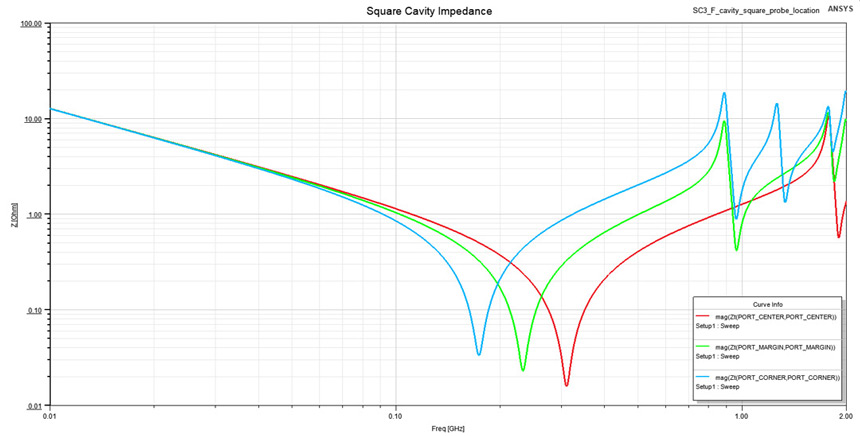
margin and corner. Observe how the SRF point capacitance changes its frequency as the
spreading inductance increases.
Approximating the impedance profile from Figure 11 with a lumped inductor on a
restricted interval between 0.4 and 0.7 GHz I extracted the value of the spreading inductance.
The results were of 144 pH for the center contact point, 337 pH for margin and 676 pH
for corner. Observe how inductance roughly doubles when the circular area where current
can spread halves. This conclusion based on simulation is in accordance with our initial
assumption about current density in the vicinity of the contact point. If we were to estimate
the spreading inductance of this square cavity using its length of 80 mm as circle diameter in
Equation 3, analytical results would be poorly correlated with simulation one, for obvious
reasons. However, from a qualitative perspective, these results would still reflect the trend
that inductance follows when probing location is changed.
The last geometry investigated in this article is also a square one with a slightly different
simulation setup used for probing the spreading inductance between two contact points. This
setup is what we would typically encounter on the design of a power distribution network
as standing between a decoupling capacitor and the pin of the integrated circuit that is
decoupled. By placing a fixed short boundary between the two planes and moving a lumped
port, the impedance profile from Figure 12 was obtained. It reveals this time in the low
frequency interval the spreading inductance between two contact points. The impact of port
size was also investigated even if in Figure 12 only results for a fixed port size of 20 MILs
are presented.
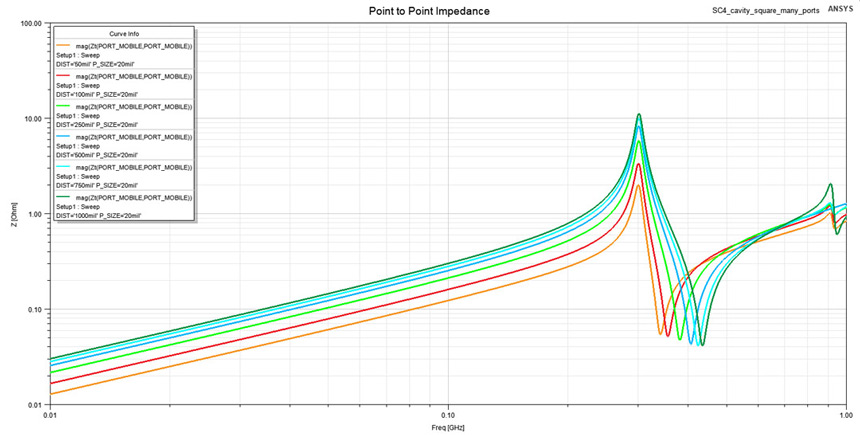
point distance is varied.
Once again by approximating a restricted interval from 100 to 50 MHz in the impedance
profile from Figure 12 with a lumped inductor I extracted the desired spreading inductance
between the two contact points. These extracted values are displayed in Figure 13 only for the
same 20 MILs port width even if more variations were studied. The complete data extracted
from this simulation profile is listed in Table 2. Observe included in this table also analytical
results obtained from Equation 5 where a k factor of 2.5 was used. These analytical values
are slightly lower than the ones obtained from the field solver for the cases of a small point
to point distance, this poor correlation being caused by current resulting from one contact
point crowding around the other, which is against the initial hypothesis of Equation 5.
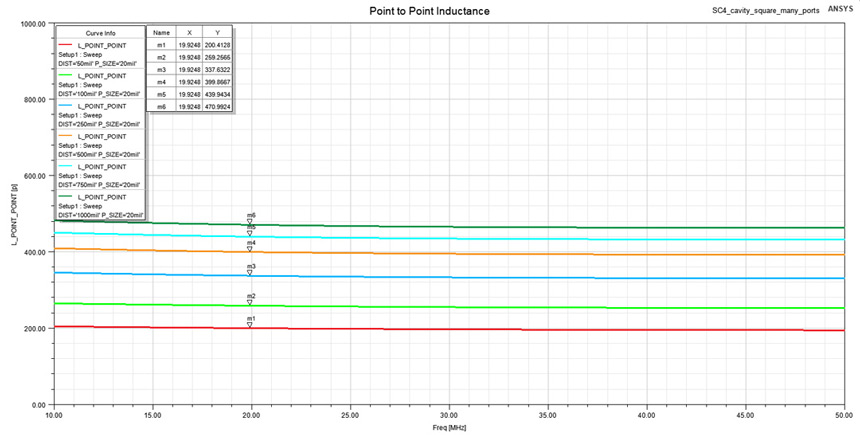
Figure 12. Notice how the inductance increases slowly when the distance between the two
points increases.
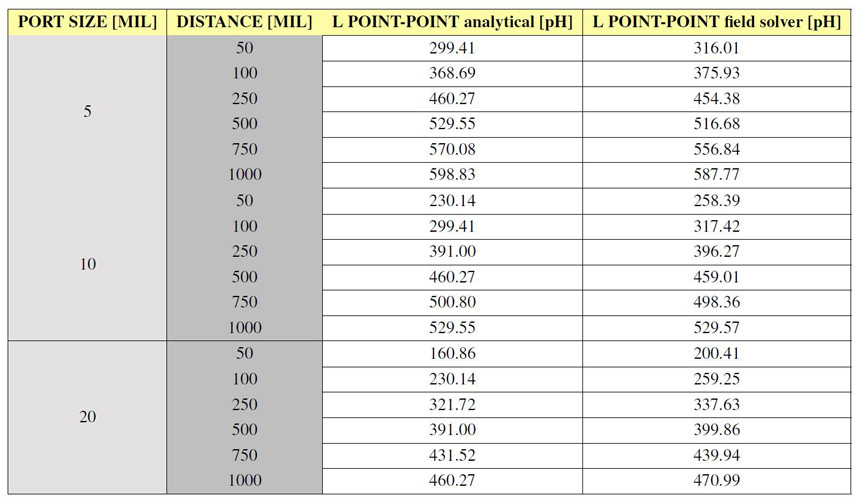
spacing and port size are varied. 3D field solver results are obtained from ANSYS HFSS and
analytical ones from Equation 5 with a value of 2.5 for the scaling factor k.
Notice from the data in Table 2 how much influence has port width on spreading
inductance: for the fixed point to point distance of 500 MILs the inductance decreases from
529 pF to 460 pF with ≈70 pF when contact size (port width) doubles. The interesting result
is that for a fixed contact size of 10 MILs, inductance also decreases with ≈70 pF from 529
pF to 460 pF when point to point distance halves. This result verifies the initial assumption
that for point to point inductance both the contact point size and the distance between points
have an equal influence.
Conclusion
In this article I investigated the second interval in the impedance profile of a cavity where it
behaves as a lumped inductor as I previously investigated the first interval where the cavity
acts like a capacitor in this previous article. Of course, these assumption that the profile
is firstly capacitive and secondly inductive are only valid if the cavity is not shorted with
VIAs, case in which the two ones are swapped. A future blog post will also analyze the third
and final interval in the impedance profile of a cavity which is dominated by resonances in
planes.
While the capacitance of two planes can easily be approximated with the parallel plate
formula, this also bears some limitations caused by the fringing effect at the margin of the
cavity. However, this limitation can be corrected when it matters, in the case of small aspect
ratio cavities. The second interval in the impedance profile of a cavity is where spreading
inductance enter the scene. Inductance is in fact a tricky and confusing concept to understand,
simulate and measure. Even if simple approximations exist for inductance, they have all
sort of limitations making them less applicable and dependent of geometry than the one for
parallel plate capacitance.
In this article I presented in depth these formulas and I correlated their results with the
one form a full-wave 3D field solver. Analyzing both the analytic and simulation results
revealed the pool of factors influencing spreading inductance. By far the most important is
the spacing between the parallel planes which should be kept as low as possible. Point to
point spreading inductance proved to be equally influenced by the spacing between points
and contact point size.
Inductance should almost always in the power integrity field be kept as low as possible
and all the methods available are to be taken in this scope as long as production cost allows it.
Closely spaced power planes and large or multiple contact points for a decoupling capacitor
can make the difference between a marginal and good PDN design.
References
Prentice Hall, 2017. ISBN 978-0-13-273555-1.
Networks. USA: Artech House, Inc., 2007. Simulation Methods and Tools. pp. 32–54.